Carbon Dioxide (CO2) extraction is a processing technique whereby CO2 is pressurized under carefully controlled temperatures to enable extraction of terpenes, cannabinoids and other plant molecules.
Green Mill Supercritical is a Pittsburgh-based manufacturing and engineering company focused on cannabis and hemp extraction. The company offers a range of CO2 extraction equipment where users can tune and control their extraction methods.
We spoke with Wes Reynolds, CEO of Green Mill Supercritical. Wes recently joined Green Mill as CEO and investor in the company after a long career at the Coca-Cola Company in senior sales and general management roles.
Aaron Green: Wes, thank you for taking the time to chat today. How did you get involved in Green Mill?
Wes Reynolds: I came out of a 20-year career at Coca-Cola, where I lived and worked around the world. I was a sales and general management guy with Coke, and learned a lot about running businesses and how to drive growth. I left Coke in 2017. After that successful career I wanted to be in the cannabis space. I felt like cannabis was a growing space with a lot of opportunity and a lot of misperceptions out there, particularly around the foundations of what I would call the “evil reputation” of cannabis. I just found that abhorrent and wanted to be part of changing it.
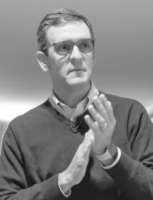
So I ran the Florida operations for Surterra, which is now called Parallel, for a year out of Tampa, and we did a great job of growing that business in Florida. As the president of the Florida operation for Surterra, I saw everything seed-to-shelf for the industry. We had a 300,000-square-foot greenhouse in Central Florida, we had dispensaries, we had all the production, distribution and all the marketing. I was really able to learn the industry top to bottom.
When I left Surterra, I started looking at various investment opportunities and thinking about what I might want to do next. I came across Green Mill out of Pittsburgh, and was really impressed with the technology that they had put together. Having run a company where we used CO2 extraction, I had experiences with systems that didn’t work when they were supposed to or didn’t work the way they were promised, which led to lots of downtime, lots of frustration and lots of babysitting. I was impressed with Green Mill’s engineering approach and decided that I’d like to be involved with them. I originally considered just being an investor, but more and more conversations led to a greater understanding of some basic business administrative needs that they had as well. One thing led to another and I agreed to come on as the CEO, and I’m also an investor.
I’m excited about what we’re doing at Green Mill. I think that bar none, we make the best supercritical CO2 extraction equipment out there. We continue to innovate on that every day. We want to push CO2 beyond known limits, which is our stated goal as a company. We believe in CO2 and we’re living our goal in that we really are pushing it beyond known limits. There are new things we’re uncovering every day where we go, “Oh, my God, I didn’t know we can do that with CO2!” So, that’s kind of fun.
Aaron: Can you tell me just a high-level overview of how CO2 extraction works?
Wes: A supercritical CO2 extraction system is a collection of extraction vessels and fractionation vessels or collection vessels. In our case fractionation because we’re doing multiple collections through a single run. Then you need a system of pumps and valves and tubing, etc. to move the solvent in a supercritical state through the packed biomass, and then move the extracted compounds into a set of collection vessels. It sounds very easy. But the key to supercritical CO2 extraction is controlling temperature, flow rate and pressure. The better you can control temperature, flow rate and pressure, the more precise of an outcome you’re going to get. For example, say you run a three-hour extraction run, and you want to run it at 3500 psi. Well, you know, a competitive system might fluctuate 300 to 400 psi on either side of 3500. Whereas our system currently fluctuates more like five to 10 psi on either side of the 3500. So, there is much more control and precision.
Our whole goal, when we’re talking about pushing CO2 beyond known limits, is how do we continue to chase that holy grail of perfect control of temperature, flow rate and pressure? One of our advances so far is a proprietary pump, for example, that’s a liquid displacement pump that we engineer and build. It ensures a very even and consistent flow, independent of the pressure setting. So, that flow rate doesn’t change in our system compared to what you would see with another system. It sounds like a minor thing, except that at the end of a run, if you expected to get a certain set of molecules, you’re going to get a different set of molecules if your temperature and flow rate and pressure are varying, because what you’re doing is disrupting the density of the CO2 as it flows.
It’s about building a system that is precise in that way, I think, that requires enormously skilled engineering effort and design effort on the front end, and then requires us to have advanced production and manufacturing capabilities in our shop in Pittsburgh. Our customers are clearly impressed with the levels of consistency that they’re getting out of their system.
Aaron: You talked about precision and consistency as two items. Is there anything else that makes Green Mill different?
Wes: I’m a brand guy. I believe in brands. I came out of a 20-year Coca-Cola career.
The way that the cannabis industry is going in total, in my opinion, is the consumer is going to get more and more discerning along the way. Up until this point, everybody thinks “oh, we have THC and CBD and we have intensity.” But the more sophisticated and educated consumers get, the more discerning they’re going to be about what products they want to put in their bodies.
What makes Green Mill different is that we’re building a system that allows the operator of that system to create differentiated products for the marketplace. So, it’s not simply “CBD is CBD.” It’s: what plant did you start with? How can you maintain as many of the characteristics of that plant as possible?
We’re going to create the most sophisticated tool possible to allow the operator to create products that can be differentiated in the marketplace for a discerning consumer at a premium price. That way, you can create a market where there might not have been a market before, instead of just “hey, I’ve got X pounds of biomass that I need to extract. Give me your bluntest instrument and let me extract.”
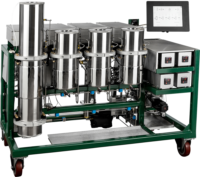
We currently make five different systems. First is the SFE Pro. We make a seven and a half liter and a 10-liter version, with two-vessel configurations of each of those. Then we have what we call a Parallel Pro, which has four 10-liter vessels and two pumps, with two streams running parallel to each other and emptying into shared collectors. It doubles the extraction rate, and you don’t expand the footprint very much. But 10-liter vessels are the biggest vessels we use. Because when you go too large with the vessel, you are giving up something in terms of the ability to control temperature, flow rate and pressure. Your efficiency starts to drop with higher vessel volume.
One of the things that makes Green Mill different is our extraction rate. Our Parallel Pro can do 145 pounds a day of biomass. We think that’s a significant amount, given the demand that’s out there for unique products. What we’re advocating for is multiple extraction systems instead of giant permanent installations of extraction systems, that end up limiting your flexibility. Big systems also prevent you from creating redundancies in your operating system. So, when your extraction system goes down, you’re done. Versus in our universe, we would say, you might want to have three or four extraction systems in different locations, running different products. Our price points are such that that’s very doable.
Aaron: How does the breakdown look between your cannabis and hemp clients?
Wes: A lot of that is legislative frankly. It has to do with what the environment is like at the moment. About 60% of our customers are small hemp farmers. And then we have the other 40% in the cannabis space that are medical or adult use producers.
CO2 extraction has a lot of applications beyond cannabis. We have a couple of customers using our system for hops extraction, for example. We see an enormous opportunity out there for non-cannabis botanical extraction, but our primary focus is cannabis. That is what we’re designing this system to do.
We find that small hemp farmers love our system because it is reliable and very automated. We have proprietary software that operates the whole system. You load and run various “recipes,” at least we call them recipes. What you are doing is setting flow rate, setting temperatures, setting pressures, etc., then that proprietary software has an unbelievable ability to control everything through the process. I’ve talked to several different operators who have used other machines, and then found themselves on a Green Mill system and couldn’t believe how easy, but also feature-rich it was.
I talk about it like it’s like an oven, you know, you set the oven at 375 degrees. And a really good oven stays right at 375. You still need to be a good chef to be able to make that perfect cheesecake. But without that oven, your hands are tied, so you are constantly trying to check those, “is it still 375? I don’t know!” With our system, if it says 375, it holds at 375. So we’re pretty excited about that.
And we’re going to continue to innovate. For example, we have a proprietary heat exchanger that we use on our systems. It’s actually 3D printed stainless steel. It’s about a 20-pound piece of steel that’s been printed to have a special tubing shape in the center only possible with 3D printing that allows us to heat CO₂ very quickly.
Aaron: That’s very cool. I’m noticing a lot actually, the innovations in cannabis are creating these adjacent market opportunities in botanicals. So, I think that’s interesting you point that out. You mentioned terpenes are one of the things you collect out of the CO2 extraction. Can you talk about the crude that comes off and how people are either monetizing or formulating that crude?
Wes: Our goal is to produce the “purest crude” possible. So, we want “less crude” crude. I think that we’re at the beginning of this, Aaron. We’re nowhere near the end, which is what I find so exciting, because all of our innovation, all of our continued development and all of our experimentation is designed to keep thinking, how do we push this further and further and further and get a more refined crude.
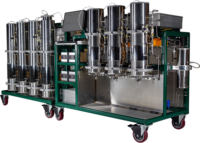
We just welcomed Jesse Turner to our team as Director of R&D, who is a well-known extraction guy in the industry. He came from Charlotte’s Web and Willie’s Reserve, and has been doing independent consulting. He’s just a rock star. He’s already off and running on experimenting with different stuff.
I think that we are just at the beginning of seeing more and more of that opportunity to help people realize, “Oh, my gosh, I did not know you could do this!” Terpenes are a good example. I think we are only scratching the surface of what terpenes can do. I mean, a cannabis plant has 400 plus molecules and we know a good bit about probably 10 or 12 of them. So, what are we going to find out about the other 390? And as we do, the Green Mill system will be ideal for separating those molecules that we don’t know today are valuable. So, I think that’s part of what we’re chasing as well.
Aaron: So where do you see CO2 extraction fitting into the cannabis and hemp supply chain?
Wes: For any product on the market that is not a smokable flower it helps to have an extraction process. There may be some products that come out that we don’t know about yet that are not going to qualify in that category. Whether you are talking about vape cartridges, or lozenges, or gummy bears, or whatever it is, they are going to start with extract. I think what consumers want is zero adulteration of their product. So if you take any botanical product, and if it is GMO-free, does not have any pesticides, maybe it is all organic, etc. — there is real consumer appeal to that. Whether you agree with it or not, it is what consumers want.
We believe that we can continue to push CO2 so that there’s no requirement for introduction of any other materials than just CO2, which is a completely inert gas. It’s got no residual effect whatsoever on the product. If we get where we want to go, then eventually you are talking about a pure botanical experience.
Initial upfront capital is higher than you are going to see with ethanol and butane extraction solutions for the same size equipment, but ongoing operating costs of those are much higher, when you weigh it out over a period of time. I think what we are going to find is that people are going to keep coming to CO2 because they realize there are things they can do with it that they can’t do any other way.
The end consumer is really who we want to keep in mind. I think for a long time, this industry was very demand driven. “I have X acres of cannabis product, whether that’s hemp, sativa, indica, whatever it is, and I need to extract this many pounds a day over this period of time.” And we keep asking the question, well, who’s going to buy that product on the other side? What do you want it to look like when you put it out on the market? As opposed to how much raw plant matter do you have? What’s the demand? And that was a difficult conversation. We’re starting to see more people come around to that conversation now. But I think that’s the question we want to keep answering is how do we create those products that are differentiated in the marketplace and that can pass muster in any regulatory environment? People are going to want to know what’s in their product.
Aaron: What trends are you following in the industry?
Wes: As the CEO, I’m particularly interested in the overall development of the landscape of the industry in terms of who’s playing, who’s winning, what’s happening with legislation, MSOs versus SSOs. I’m also interested in the international environment. We have a good bit of interest from multiple countries that have either ordered Green Mill systems or are talking to us about Green Mill systems, including Canada and Latin American countries, some European countries, Australia and New Zealand.“We’re really committed to educational efforts with a very rigorous scientific foundation, but in language that is approachable and people can understand.”
The trends that I’m particularly interested in are more on the business side of the equation, in terms of how this business is going to shake out particularly from a capitalization perspective, as banking laws continue to change, which is a big deal, and the legislative environment gets a little more predictable and a little more consistent.
Aaron: Okay, last question. So what are you personally interested in learning more about?
Wes: Everything, is the short answer! I constantly run this little challenge of trying to understand enough of the science. I’m not a scientist, I’m a sales guy. That was how I grew up: general management and sales. I’ve made my living over many years being wowed by the pros. Depending on the scientists and the very specialized folks to help provide the right answers to things. I’m fascinated by the chemistry and I’m fascinated by the mechanical engineering challenges of what we do at Green Mill. So, I’m always interested in learning about that.
I think there’s a need, and it is helpful to be able to talk about those things in language that the layperson can understand, as opposed to explaining everything in scientific language. I think what I am trying to do is help people put it into a language that they can get, but that is not simple. Language that is correlative to reality. I think there’s so much misunderstanding about how these things work and what’s happening. We’re really committed to educational efforts with a very rigorous scientific foundation, but in language that is approachable and people can understand.
Aaron: Okay, that’s it. Thank you for your time Wes!